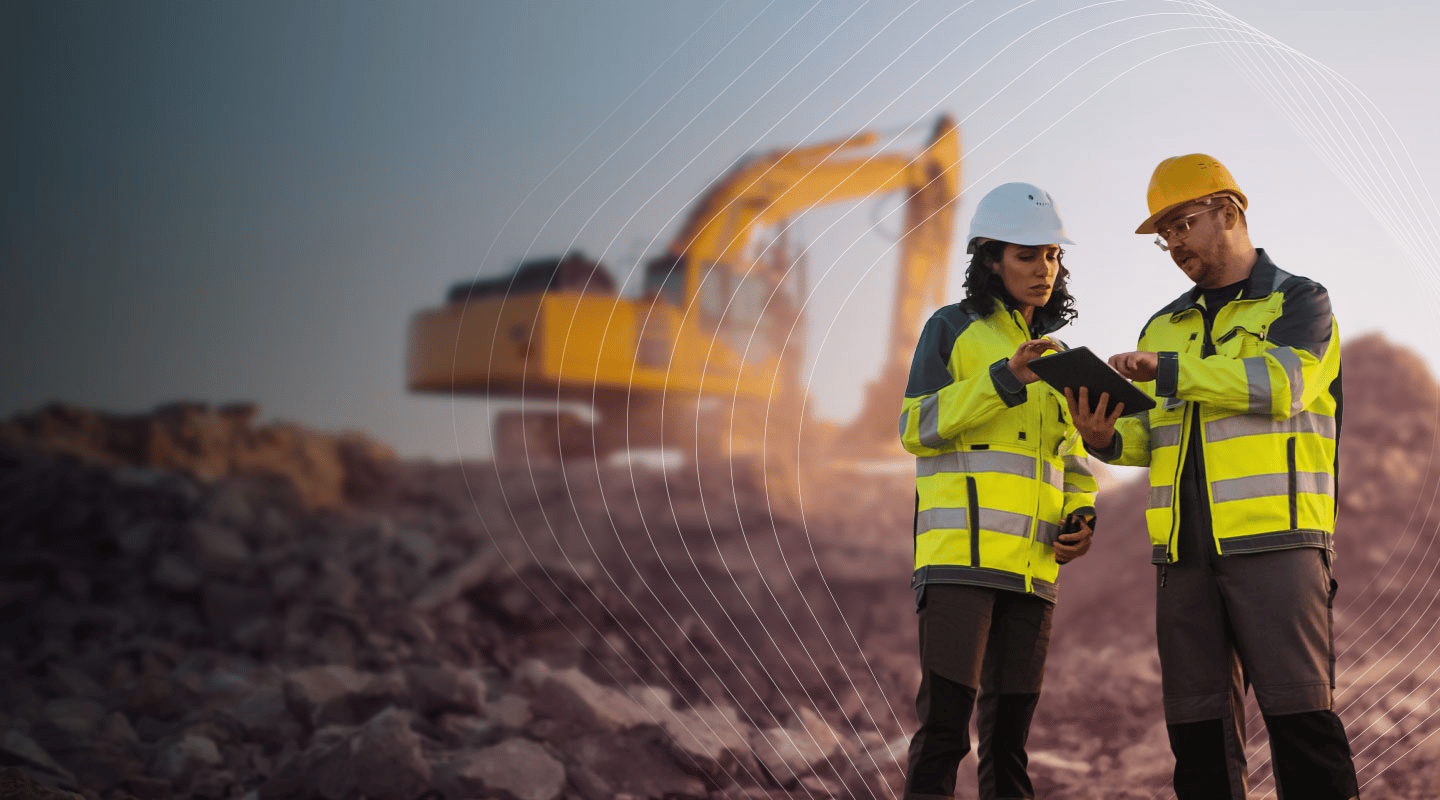
Trusted by:
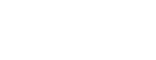
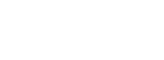
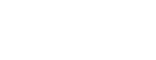
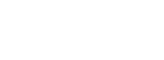
Maximize efficiency, stop price erosion, win deals
One platform for rental equipment
Whether you’re a contractor, rental company or similar, we got you covered. Read each of our use cases below!
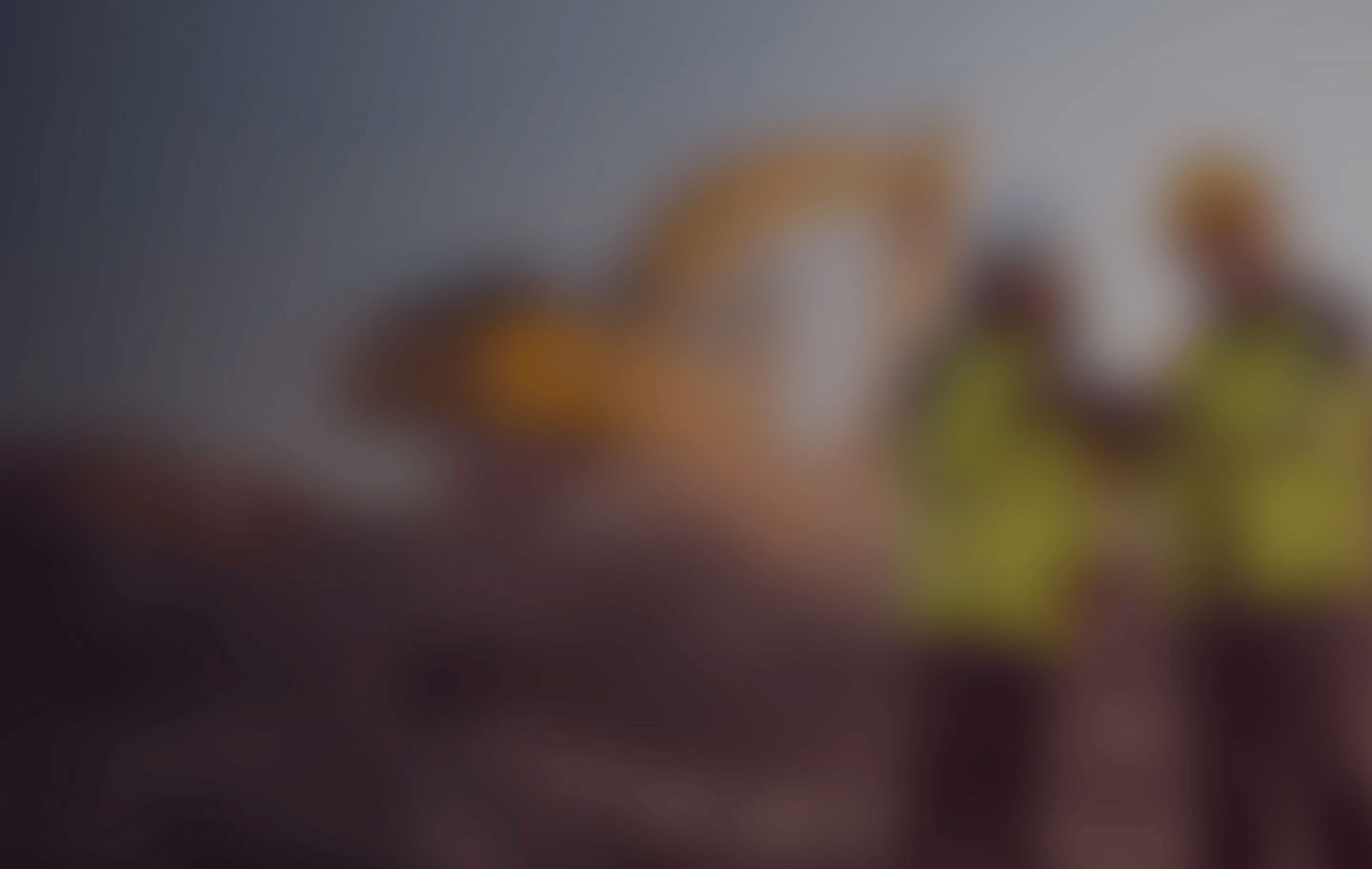
Make sales easier using our tools
ROI calculators
Presentations
Demo app
Become your contractors’ trusted advisor
Optimize equipment utilization and capacity
Use jobsite live data on rental behavior, utilization rates and other KPIs to help contractors optimize equipment. Become a trusted advisor on the type of machine needed and in which quantity, at every stage of the project.
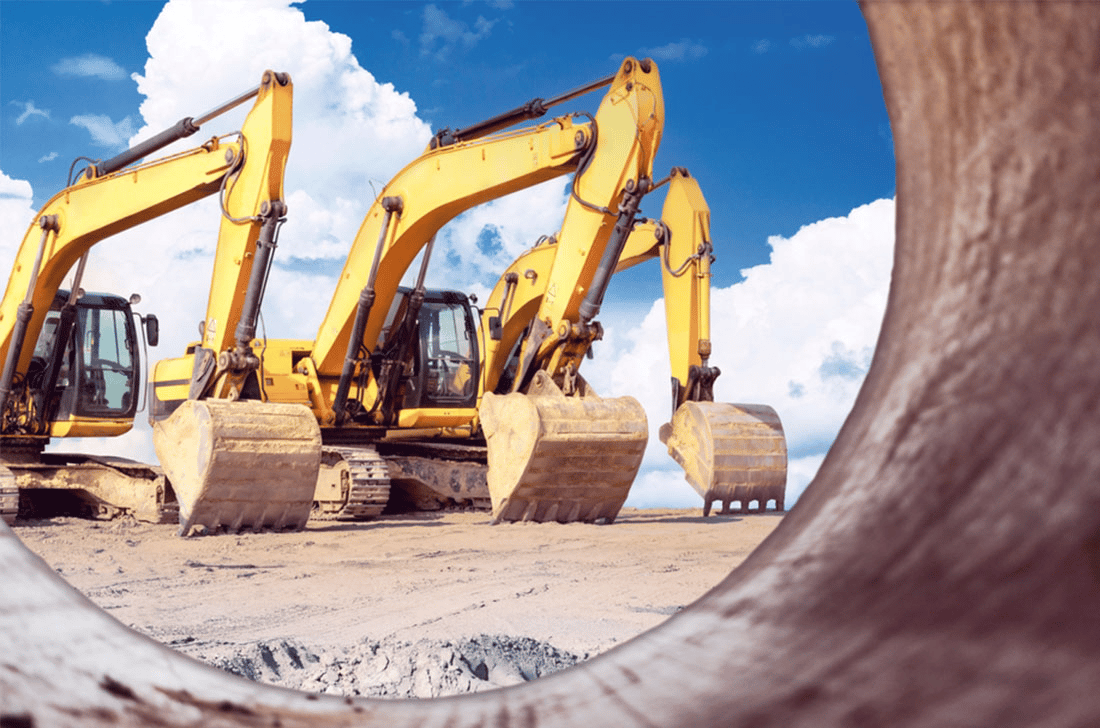
Discover valuable insights
Advise contractors on how to understand their projects better, improving their rental fleet productivity, safety, efficiency and sustainability. Become the preferred supplier on any project.
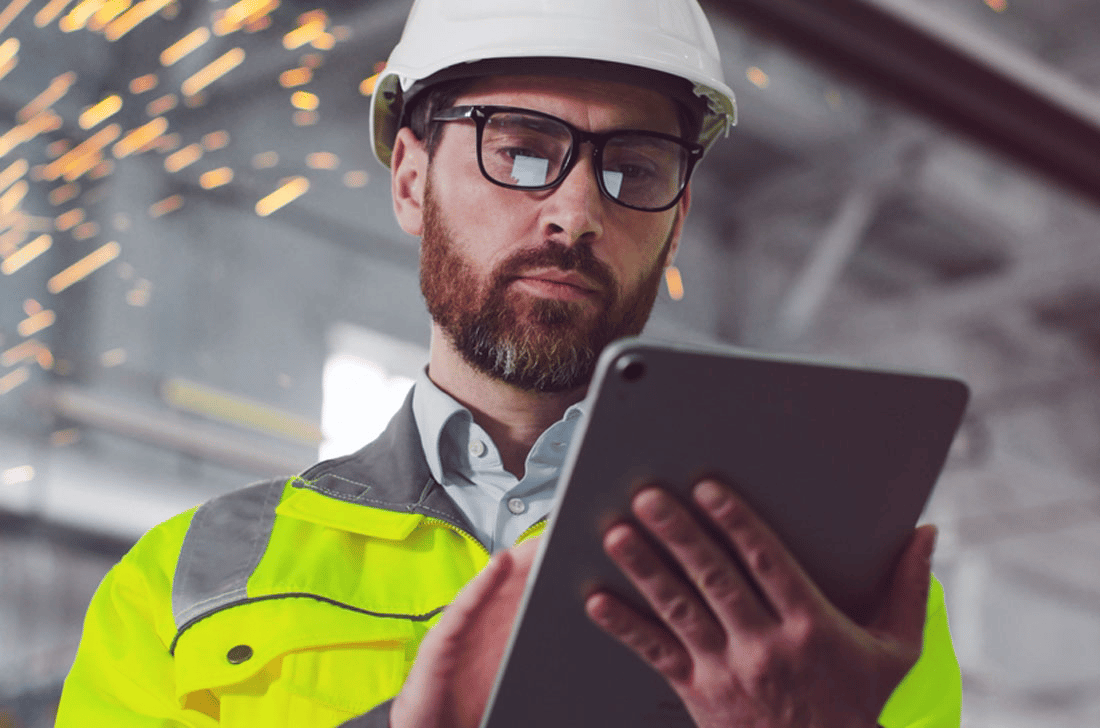
Remotely monitor equipment condition
Check equipment condition remotely using reports and notifications. Maximize equipment up-time while ensuring contractors have quality equipment and the best possible rental experience.
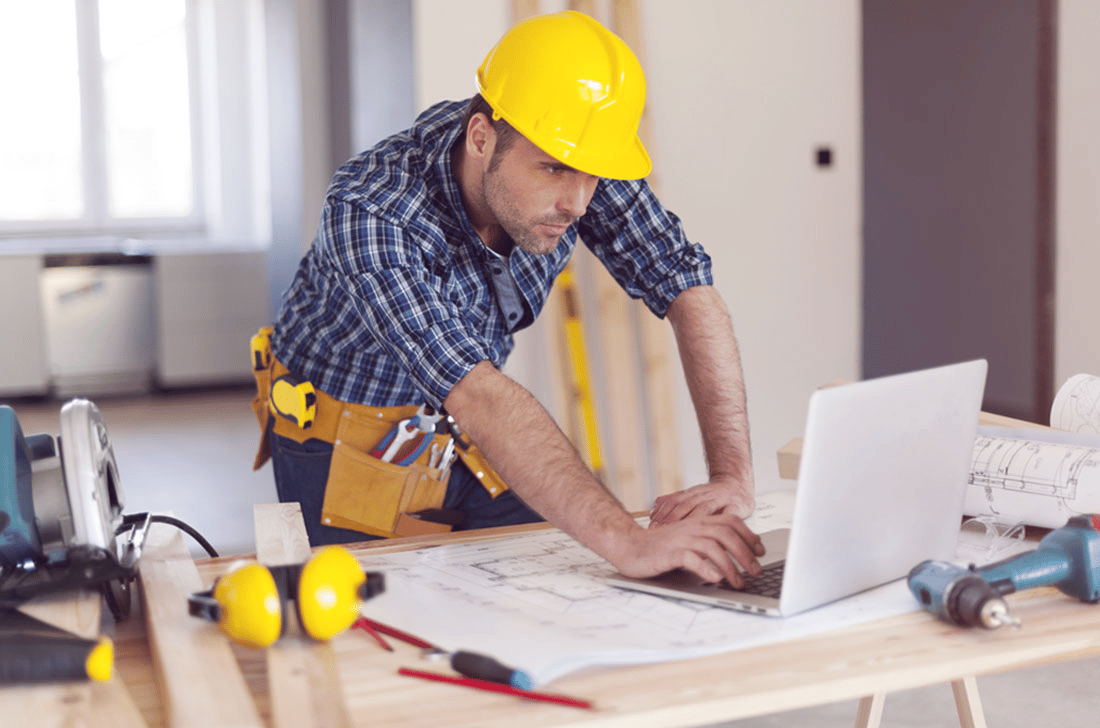
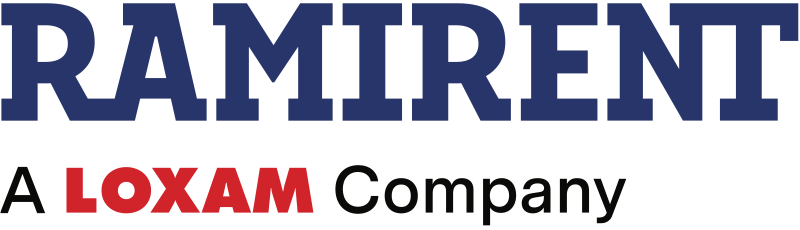
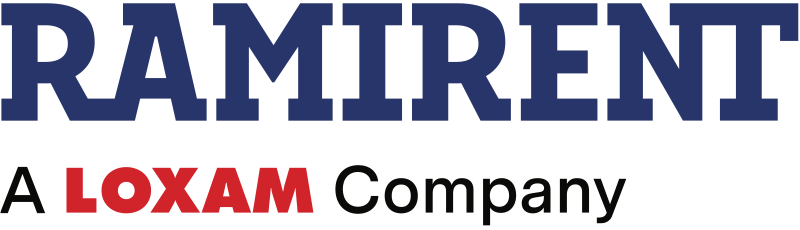
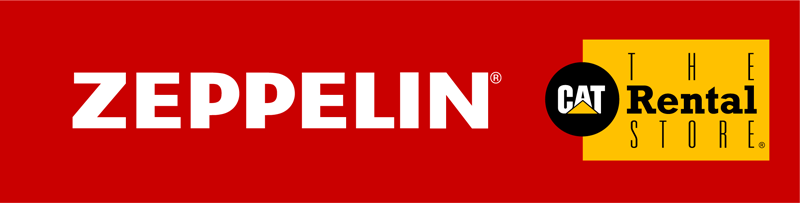
Latest insights in our knowledge base
We love sharing our knowledge and expertise. Below are some recent examples
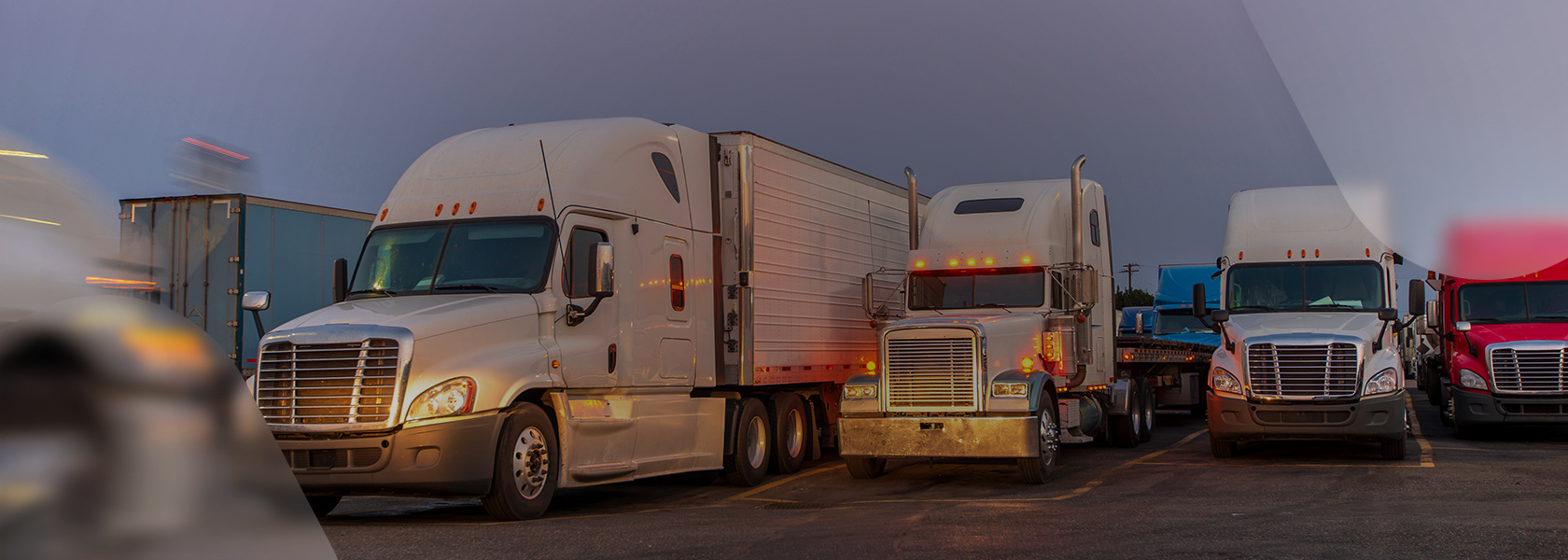
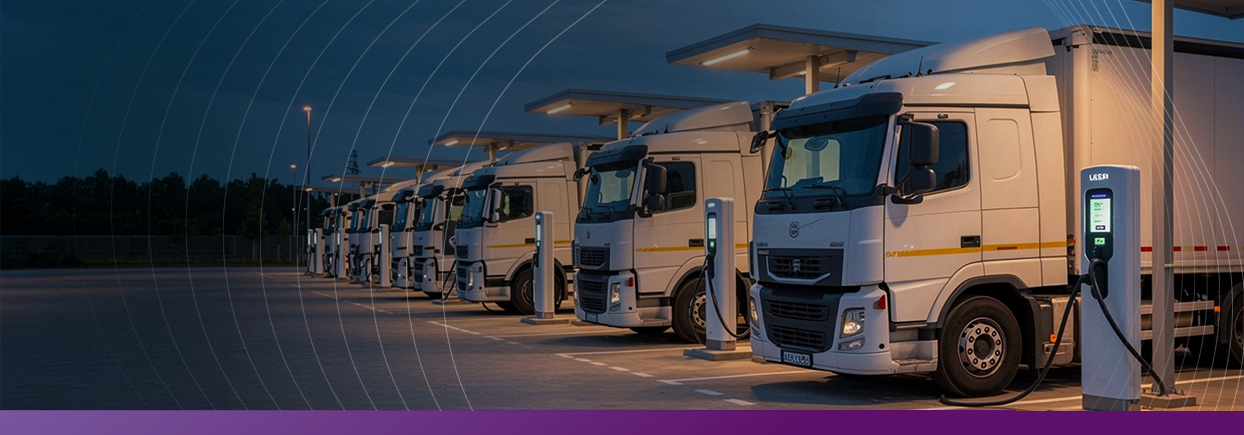
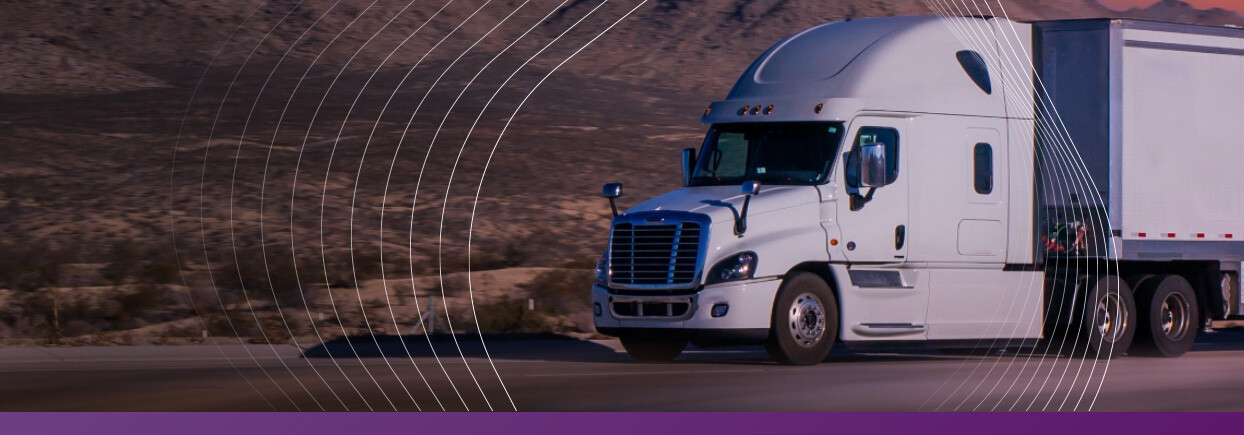
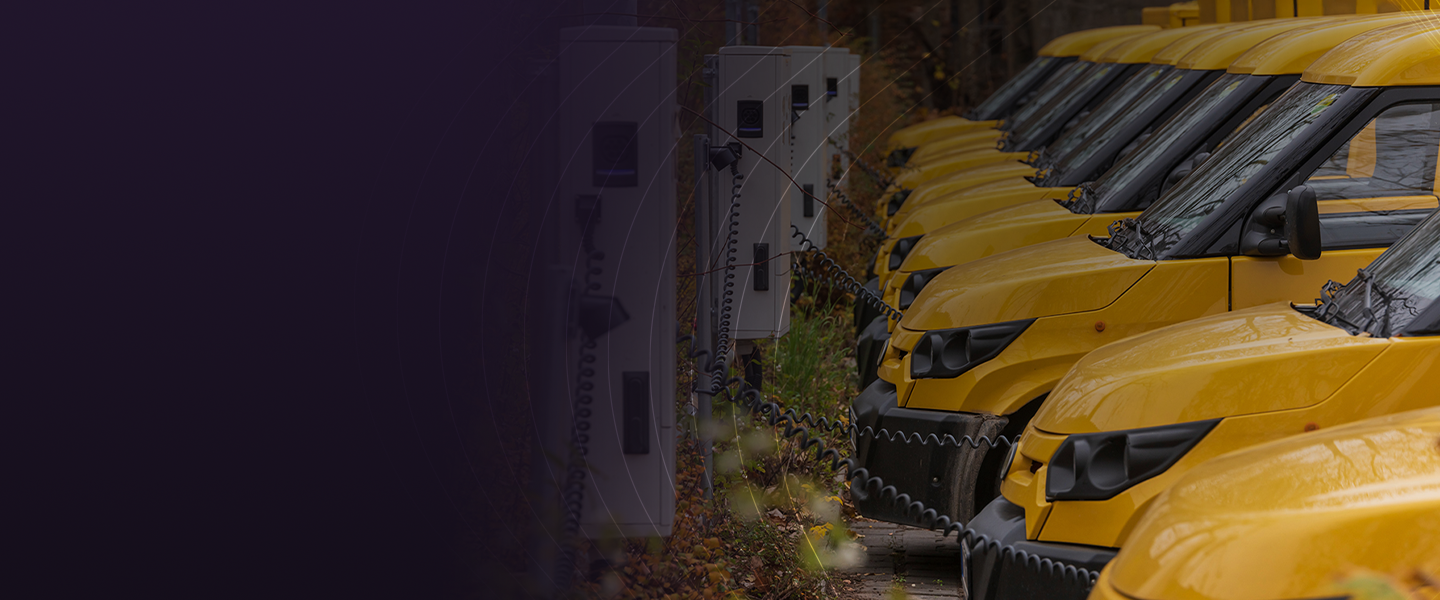
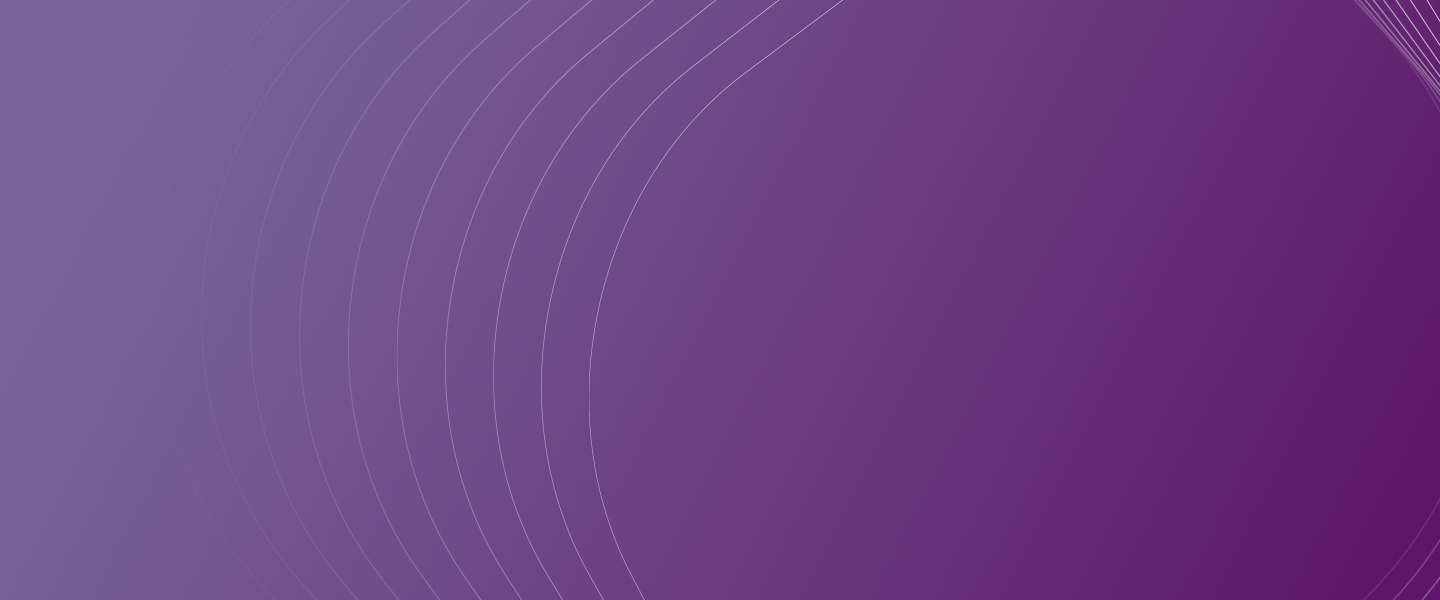
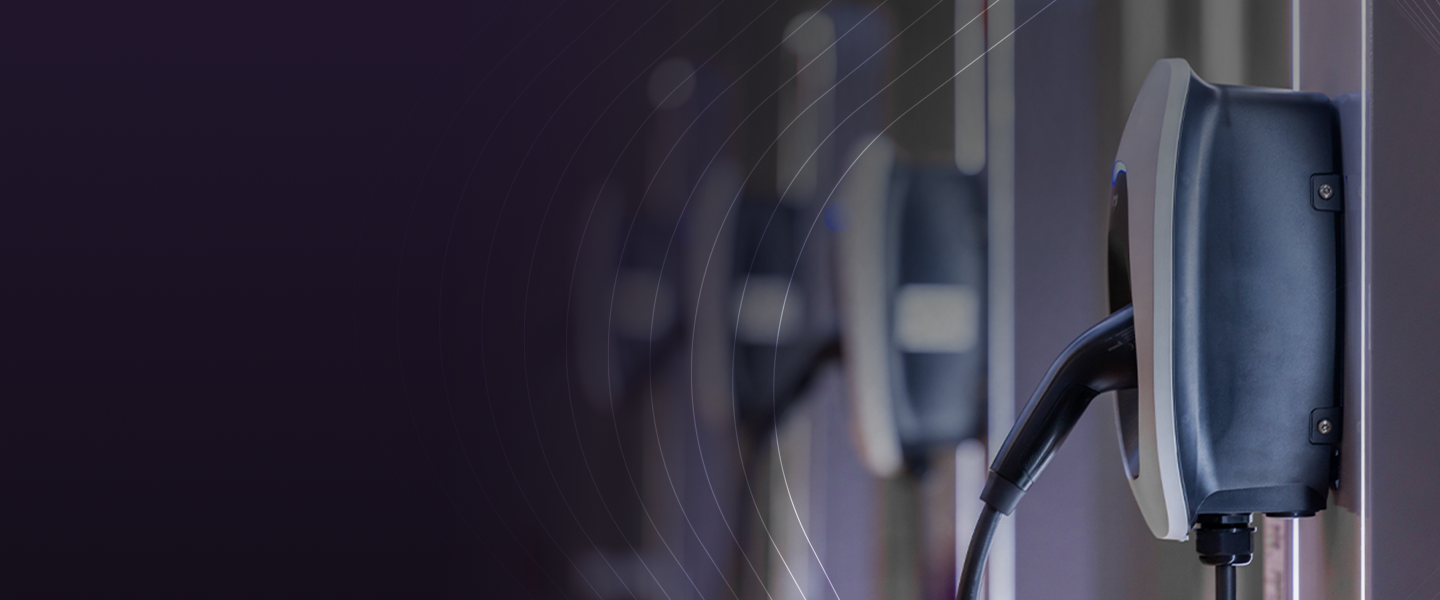